Digital Twins and Their Role in Accelerating Product Engineering
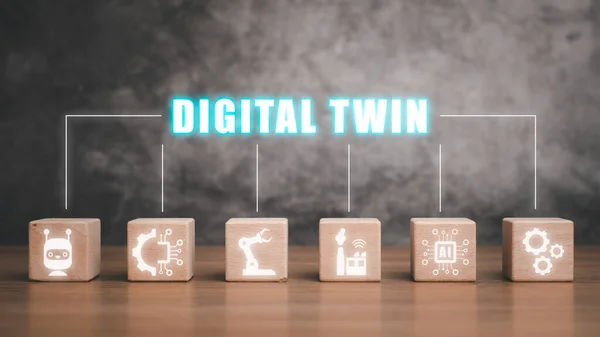
In today’s rapidly evolving technological landscape, innovation drives competition and success. Among the cutting-edge technologies reshaping how products are designed and developed, digital twins stand out as a transformative tool in the product engineering space. From optimizing designs to monitoring performance in real-time, digital twins have the potential to significantly accelerate product engineering by bridging the gap between physical and digital worlds.
In this blog, we’ll explore what digital twin technology is, how it enhances product design and development, and its applications across various industries.
What is Digital Twin Technology?
A digital twin is a virtual representation or simulation of a physical object, process, or system. It mirrors its real-world counterpart in real-time, enabling businesses to monitor, analyze, and optimize the product throughout its lifecycle. Digital twins are created by integrating data from sensors, IoT devices, and other systems with machine learning models and simulations. This results in a dynamic, data-driven replica that evolves with the physical object.
By allowing companies to test and refine products in a virtual environment, digital twins reduce risks, cut costs, and speed up the time to market. The ability to continuously improve and update products based on real-time data leads to greater efficiency and better decision-making.
How Digital Twins Enhance Product Design and Development
1. Prototyping and Testing: Traditionally, product development involved physical prototyping, which could be time-consuming and costly. Digital twins enable engineers to create and test virtual prototypes, allowing for faster iterations. Engineers can simulate different scenarios, test the product under various conditions, and optimize designs without having to build multiple physical prototypes. This accelerates the design process while reducing development costs.
2. Predictive Maintenance and Reliability: Digital twins are valuable not only during the product development phase but also throughout the product's lifecycle. By monitoring the real-time data of physical assets, businesses can use digital twins for predictive maintenance. This means potential issues can be detected before they lead to failures, improving the reliability of products and reducing downtime.
3. Continuous Product Improvement: Digital twins provide a constant feedback loop by integrating data from IoT sensors and customer usage. This enables companies to continuously monitor product performance and make informed decisions on upgrades or improvements. The data-driven insights gathered from digital twins ensure that products evolve based on real-world data, creating opportunities for constant optimization and refinement.
4. Customization and Personalization: One of the most exciting aspects of digital twins is their potential to support customized and personalized products. With digital twins, businesses can simulate different versions of a product based on individual customer needs, ensuring that the final product is tailored precisely to the user’s requirements. This approach to customization drives customer satisfaction and enhances product value.
Applications of Digital Twins Across Industries
Successfully building and managing SaaS and PaaS products requires thoughtful planning and execution. Here are best practices to follow:
1. Manufacturing: In the manufacturing industry, digital twins play a pivotal role in optimizing production processes. By simulating factory floors, machinery, and workflows, manufacturers can identify bottlenecks and inefficiencies in their processes. Digital twins also enable predictive maintenance of equipment, improving machine reliability and minimizing downtime, leading to more efficient and cost-effective operations.
2. Healthcare: The healthcare industry is leveraging digital twins to improve patient outcomes. Digital twins of medical devices, such as pacemakers or MRI machines, allow for continuous monitoring and predictive maintenance, ensuring optimal performance. In advanced applications, digital twins of human organs or entire systems could allow doctors to simulate surgical procedures or treatment plans, resulting in more precise and personalized healthcare.
3. Automotive: In the automotive sector, digital twins help design, test, and optimize vehicles before they are even built. Manufacturers can simulate the performance of different vehicle components, such as engines or braking systems, under various conditions. This accelerates the development of new models and ensures that vehicles meet safety and efficiency standards. Additionally, digital twins enable real-time monitoring of vehicles on the road, allowing for predictive maintenance and enhanced vehicle performance.
4. Smart Cities: Digital twins are revolutionizing urban planning and infrastructure management. Cities can create digital replicas of buildings, transportation systems, and utilities to simulate urban growth, traffic flow, and energy consumption. This allows city planners to make informed decisions about infrastructure improvements, optimize resource usage, and enhance the quality of life for residents.
5. Aerospace: In aerospace engineering, digital twins are used to model the performance of aircraft and spacecraft components, enabling engineers to identify potential issues before they arise. For example, the digital twin of an engine can simulate wear and tear over time, allowing for more accurate maintenance schedules and ensuring that aircraft operate at peak performance levels. This reduces the risk of in-flight failures and enhances safety.
6. Energy: In the energy sector, digital twins are used to optimize the performance of assets such as wind turbines, solar panels, and power plants. By simulating different environmental conditions and usage patterns, energy providers can predict the best times for maintenance and maximize energy output. The use of digital twins also enables better energy grid management, ensuring efficient energy distribution across regions.
The Future of Digital Twins in Product Engineering
As industries continue to embrace digital transformation, the adoption of digital twins is expected to grow significantly. The integration of AI and machine learning into digital twin platforms will enhance their predictive capabilities, making product development and management even more precise. Companies that leverage digital twins will be able to reduce costs, minimize risks, and deliver better-performing products to market faster than their competitors.
The ability to simulate, test, and optimize products in a virtual environment not only speeds up the development process but also allows for more sustainable innovation. Digital twins support a future where companies can design products that are smarter, more reliable, and customized to meet evolving customer demands.
Conclusion
Digital twin technology represents a powerful tool in accelerating product engineering. From prototyping to predictive maintenance and beyond, the ability to create virtual replicas of physical assets allows businesses to design, test, and improve products with unparalleled efficiency. The benefits of digital twins stretch across industries, transforming how companies approach innovation and product development.
At Raphus Solutions, we are dedicated to leveraging the power of digital twins to help businesses achieve faster product development cycles, improved reliability, and enhanced customer experiences. By embracing this cutting-edge technology, enterprises can stay ahead of the curve in an increasingly competitive marketplace.